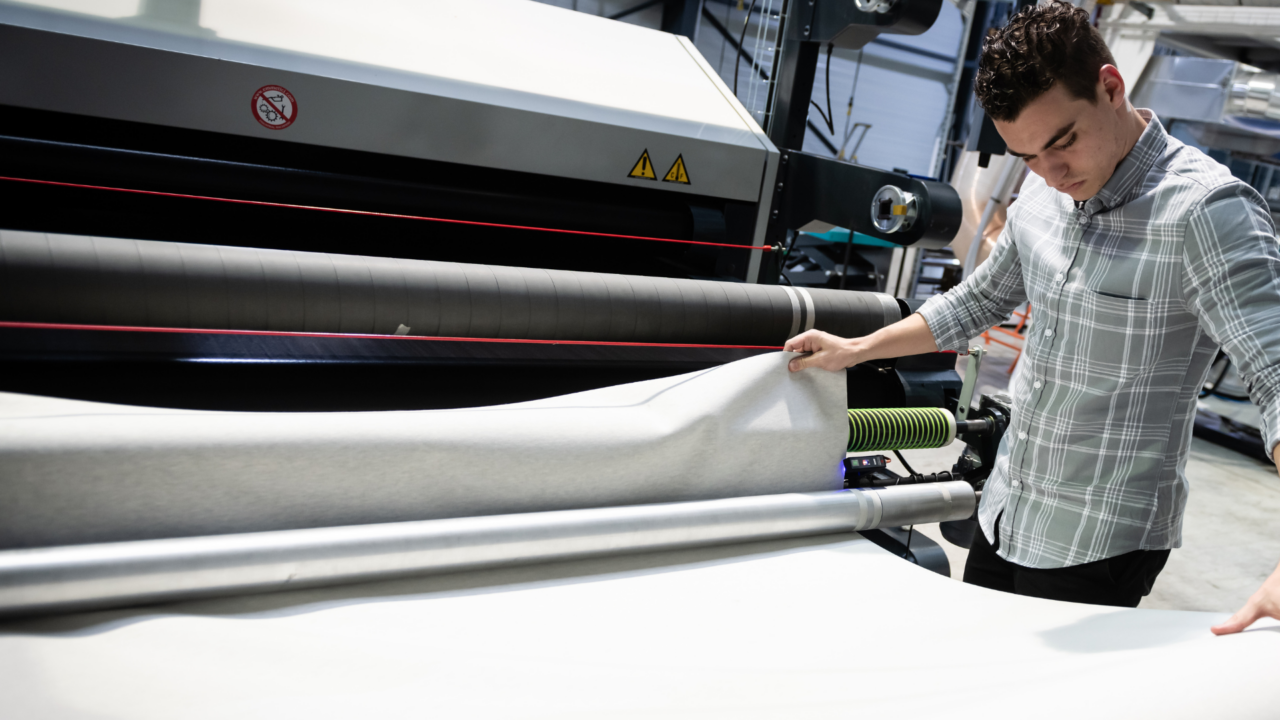
Thermoplastic adhesives offer an alternative to traditional bonding methods. However, achieving optimal results requires consideration of a range of factors that can influence bond strength.
Here, we will talk about the most common challenges met in thermoplastic bonding and explore strategies to ensure a successful assembly process.
Surface Preparation
Just like any bonding technique, surface preparation is critical for achieving a strong and reliable bond with thermoplastics. Overlooking this step can lead to weak or uneven adhesion. Common mistakes include:
- Insufficient cleaning: Residual contaminants like dust and oil or release agents can compromise the adhesive’s ability to form a proper bond with the substrate(s). Ensure a consistent cleaning process using appropriate solvents or degreasers according to the specific materials involved.
- Surface modification: Certain materials may require additional surface pre-treatment such as corona treatment, plasma treatment, surface primer in order to increase the surface energy of the materials and allow the adhesive to achieve a good bond.
Inconsistent Bond Line Thickness
Maintaining a uniform bond line thickness is essential for achieving an even and consistent adhesion throughout the bonded construction. Variations in thickness can create weak points where there is a lack of adhesive weight, leading to premature bond failure under pressure or mechanical strain.
Here is how to address this issue:
Adhesive selection: The viscosity and flow characteristics of the chosen adhesive should be compatible with the desired bond line thickness and application method.
Inadequate Laminating Process Parameters
Thermoplastic bonding relies on precise control of temperature, pressure, and time. Deviations from the recommended parameters can negatively impact bond strength.
Common issues include:
- Improper temperature control: Insufficient heat activation can prevent the adhesive from reaching its optimal flow state, leading to a weak bond. Conversely, excessive heat can degrade the adhesive or damage the substrates.
- Insufficient pressure: Inadequate pressure during the bonding process can result in weak adhesion. Conversely, excessive pressure might cause the adhesive to penetrate too deeply into the materials compromising the final bond strength and also alter the visual aspect and hand feel of the laminated product.
- Incorrect time: Insufficient time might not allow all components of the adhesive to fully melt and form a strong bond with the substrates. Conversely, excessive dwell time can lead to thermal degradation of the adhesive or the substrates.
Optimizing Your Thermoplastic Bonding Process
By carefully addressing these potential pitfalls, manufacturers can ensure a robust and reliable thermoplastic bonding process. Here are some additional tips for success:
- Material compatibility testing: Thorough compatibility testing between the chosen adhesive and substrates is essential to ensure proper adhesion and prevent unexpected bond failure at a later stage.
Substrate-adhesive interactions can significantly impact bond strength over time. Factors like plasticizer migration from materials can weaken the bond, leading to delamination. Proper testing helps mitigate these risks.
- Process validation: Once the optimal parameters are identified, validate the entire bonding process through adequate testing and industrial trials to guarantee consistent and reliable results on a production scale.
- Partner with an expert: Collaborate with a reputable thermoplastic adhesive supplier who can provide technical support and recommend the most suitable adhesive solution for your specific application.
If you would need technical guidance for you bonding project, contact our expert team at:
commercial@protechnic.bemisworldwide.com
Our technical support team is mobile and can help wherever you are located.